In a world first, Laserline’s new blue diode lasers of up to 6kW demonstrate advantages over infrared lasers for industrial work with reflective metals such as gold or, importantly, copper. Copper is now recognised by many countries as a critical mineral because it’s integral to low-emission technologies such as electric vehicles, batteries, solar panels, wind turbines and general electrification.
Low energy absorption by highly reflective metals is a problem for standard near-infrared (NIR) lasers emitting around 1,000 nanometres (nm) wavelength. High intensities of laser power that are initially needed by IR lasers often create turbulent melt pools and spatters that lead to low-quality weld seams.
Dr Cedric Chaminade, Technical Director at Raymax Applications which distributes Laserline equipment in Australasia, says blue diode lasers increase the power absorption of the beam, hence efficiency too, beyond that of IR laser processes.
“The blue diode laser has been shown to be absorbed by copper alloys at five times greater than near-infrared wavelengths,” says Cedric. “The result is a more energy-efficient and material-efficient process.”
“At about 445 nanometres, Laserline’s latest blue lasers offer an ideal wavelength for processing highly reflective metals.
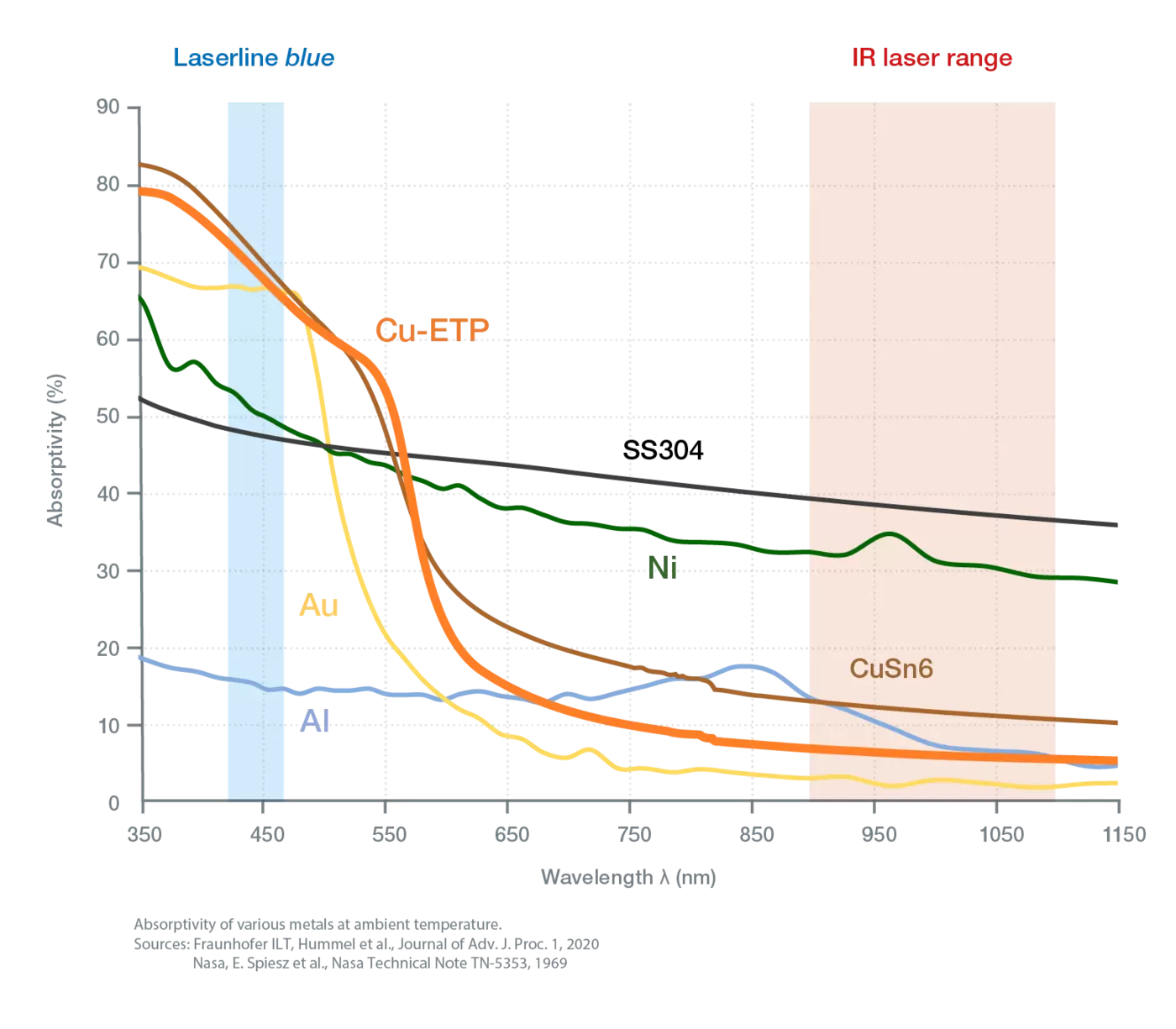
“Thanks to reflective materials’ higher absorption of the blue beam, these blue diode lasers achieve a smooth, stable and simple process that leads to reproducible results without spattering.
“Efficiency is boosted because laser generation from diodes is direct – at up to 6kW continuous wave laser power at 445 nanometres wavelength – so there’s no need for any detour via complex and inefficient wavelength conversions.”
The 6kW blue diode laser was released late last year at the additive manufacturing expo Formnext in Germany. Extensive welding tests over the past couple of years have shown stable melt pools without turbulence or pore formation and a consistent weld depth. In contrast, IR lasers require smaller spots and higher power densities for coupling with copper surfaces, create inferior welding depth, higher turbulence and porosity.
Energy deposition by blue diode lasers can also be precisely controlled to enable copper to be melted without evaporation, resulting in previously unattainable melt-pool stability.
“This opens possibilities for new applications such as heat-conduction welding of thin copper foils, spatter-free welding of electrical connectors and also 3D printing of copper parts,” says Cedric.
Advantages
- Up to 6,000 W laser power (cw) at a wavelength of approx. 445 nm
- Optimised absorption for highly reflective metals
- Scanner or fixed optics for optimum beam guidance
- Flexibility of the process optics for lines and surfaces
- Field-proven system architecture
- Optional two-exit beam switch
- Very stable process with smooth, melt-bath properties
If you’re keen to hear more about Laserline’s blue diode lasers, please call Dr Cedric Chaminade, Raymax’s Technical Director, on (+61 2) 9979 7646.